本文目录一览
1,混凝土离析要怎样处理2,混凝土离析的原因及补救方法3,混泥土出现离析泌水的原因是什么4,什么是混凝土的离析现象5,混凝土离析现象6,什么是混凝土拌合物的离析和泌水7,混凝土离析8,什么是混泥土离析
1,混凝土离析要怎样处理
一般时候,在离析的情况下,进行适当的搅拌,就能回复。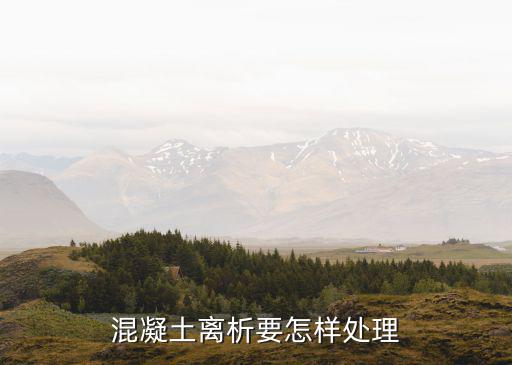
2,混凝土离析的原因及补救方法
混凝土离析的原因及补救方法,内容如下:混凝土离析原因有:水泥质量差、骨料导致离析、外加剂的原因、设备故障原因等。混凝土离析的补救方法:1、对于因骨料含水率问题造成的混凝土离析,因采取延长搅拌时间的手段来解决提高粉煤灰等掺合料的用量,对于控制这类问题也有效。 2、在施工过程中要严把质量关,坚决杜绝不合格材料进入施工现场,保证骨料的质量稳定。3、如果沙子中的含水量处于饱和状态时,可采取延长搅拌时间手段去解决或提高粉煤灰的等掺合料用量。 4、提高砂率来调整混凝土配合比也是可以解决离析。混凝土离析问题,主要原因是停的时间过长没有搅拌,或水灰比过大形成。处理方法一般情况下第一种现象普遍要及时搅拌做坍落度试验,待坍落度试验合适了方可正常施工。若水灰比过大要及时调整用水量多少最好有计量水量的工具或表。混凝土离析,主要是指混凝土拌合物组成材料之间的粘聚力不足,粗骨料下沉的一种现象。一般情况下,如果混凝土中分泌出了大量的水,基本上能够确定,混凝土已经发生了离析。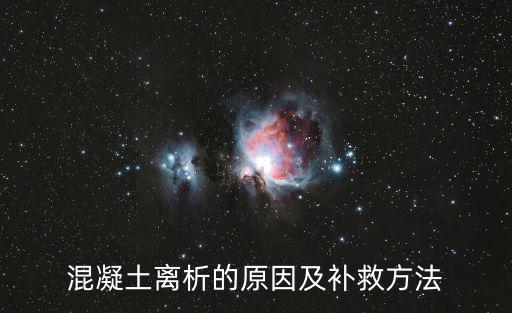
3,混泥土出现离析泌水的原因是什么
我来回答水泥细度大时易泌水;水泥中C3A含量低易泌水;水泥标准稠度用水量小易泌水;矿渣比普硅易泌水;火山灰质硅酸盐水泥易泌水;掺Ⅰ级粉煤灰易泌水;掺非亲水性混合材的水泥易泌水。
4,什么是混凝土的离析现象
混凝土离析是指粗骨料与细骨料分离。 离析后会影响混凝土的浇筑质量,降低强度,造成粗骨料堆积,形象的说就是骨肉分离。 混凝土搅拌时配合比计量要准确,保证搅拌时间一般为90s,控制好坍落度,混凝土自由下落高度不能超过2m,如果浇筑超过2m的可以用溜槽,溜筒等辅助工具。5,混凝土离析现象
离析就是骨料分离。如果塌落度合适要解决就增加下胶才用量,调整水灰比。如果塌落度高于设计值就减水看看。。。离析现象是由于混凝土配合比设计不当造成的 有关的详细的资料请来www.stonw.com查看6,什么是混凝土拌合物的离析和泌水
1、混凝土拌合物的离析:配制流态混凝土时,流动性和粘聚性失去平衡,当粘聚性低时混凝土在自身重力或其它外力作用下产生相分离,破坏了材料组成的均匀性和稳定性,导致分离这就是离析。2、混凝土拌合物的泌水:混凝土在运输、振捣、泵送的过程中出现粗骨料下沉,水分上浮的现象称为混凝土泌水。泌水是离析的前奏,离析必然导致分层,增加堵泵的可能。少量泌水在工程中是允许的,而且对防止产生混凝土表面裂缝有利。3、离析和泌水产生的原因:1)、砂率偏低或砂子中细颗粒含量少使混凝土保水性低,砂子含泥量大易产生浆体沉降,即“抓底”;2)、胶凝材料总量少,浆体体积小于300L/m3;3)、石子级配差,或单一粒径的石子;4)、用水量大,使混凝土拌合物粘性低;5)、外加剂掺量过大,或外加剂黏度低保水性不佳;6)、使用矿渣或矿渣水泥,本身保水性不好,易泌水、离析。7,混凝土离析
原发布者:lvxuefeng5188什么是混凝土的离析现象?混凝土离析是指粗骨料与细骨料分离。离析后会影响混凝土的浇筑质量,降低强度,造成粗骨料堆积,形象的说就是骨肉分离。混凝土搅拌时配合比计量要准确,保证搅拌时间一般为90s,控制好坍落度,混凝土自由下落高度不能超过2m,如果浇筑超过2m的可以用溜槽,溜筒等辅助工具。混凝土拌和物离析的定义,形式及产生原因?上下密度不一,(下大上小)粗细骨料分布不均,混凝土坍塌度过大。形式表现为下面都是粗骨料。中间是细骨料。上面是沙浆。最上面是水。原因是在搅和混凝土的过程中参水比例过大。混凝土离析和泌水的定义1.混凝土离析是指粗骨料与细骨料分离。离析后会影响混凝土的浇筑质量,降低强度,造成粗骨料堆积,形象的说就是骨肉分离。混凝土搅拌时配合比计量要准确,保证搅拌时间一般为90s,控制好坍落度,混凝土自由下落高度不能超过2m,如果浇筑超过2m的可以用溜槽,溜筒等辅助工具。2.混凝土在运输、振捣、泵送的过程中出现粗骨料下沉,水分上浮的现象称为混凝土泌水。泌水是新拌混凝土工作性一个重要方面。通常,描述混凝土泌水特性的指标有泌水量(即混凝土拌和物单位面积的平均泌水量)和泌水率(即泌水量对混凝土拌和物之比含水量之比)。混凝土施工泌水的原因是什么?当前工程施工中发现混凝土有分层离析现象,怎么解决啊?在混凝土施工过程中,通常会出现在运输、振捣、泵送的过程中出现粗骨料下沉,水分上浮的现象称为混凝土泌水。泌水是新拌混砼离析是指泵送剂掺量超过了其胶凝材料的饱和点,而导致胶凝材料颗粒之间的阻力减小,位移加快的状况。混凝土离析的现象是:当商品混凝土拌合物堆成一堆时,砼拌合物的流动性很好,在一分钟或较长一点的时间内,拌合物表面泌出稀浆向边缘流出,表面露出石子,并且石子表面不沾砂浆。砂石下沉紧贴底板,用铁锨很难铲动,这种现象也叫扒底。回答:1,水灰比过大会造成混凝土坍落度过大,用句白话就是稀了,水大了,水大了以后混凝土的和易性就不好,大骨料得不到水泥等结合料的制约,就会下沉,从而导致了离析,2,粗骨料粒径大,集料级配不良导致离析的原因是一样的,在混凝土中集料级配良好的时候各种骨料会形成一个整体,小料填补大料的缝隙,砂填补小料的缝隙水泥浆将这些结合起来才形成了混凝土集料级配不良时个材料形成不了整体当然离析。3减水剂掺量大的话就太干了,一样不合适。你问的问题太过肤浅和无趣,混凝土水灰比,粗骨料粒径都是有相应的标准的,一般是通过实验找到最佳配比,因为各地所用水泥的差异,配比一般是有较大的差异的。8,什么是混泥土离析
混凝土的离析是混凝土拌合物组成材料之间的粘聚力不足以抵抗粗集料下沉,混凝土拌合物成分相互分离,造成内部组成和结构不均匀的现象。通常表现为粗集料与砂浆相互分离,例如密度大的颗粒沉积到拌合物的底部,或者粗集料从拌合物中整体分离出来。离析的原因造成离析的原因可能是浇筑,振捣不当,集料最大粒径过大,粗集料比例过高,胶凝材料和细集料的含量偏低,与细集料比粗集料的密度过大,或者拌合物过干或者过稀等。使用矿物掺合料或引气剂可降低离析倾向。离析的危害影响混凝土的泵送施工性能,造成粘罐、堵管、影响工期等,降低经济效益。影响混凝土结构表观效果,混凝土表面出现砂纹、骨料外露、钢筋外露等现象。使混凝土强度大幅度下降,严重影响混凝土结构承载能力,破坏结构的安全性能,严重的将造成返工,造成巨大的经济损失。混凝土的匀质性差,致使混凝土各部位的收缩不一致,易产生混凝土收缩裂缝。特别是在施工混凝土楼板时,由于混凝土离析使表层的水泥浆层增厚,收缩急剧增大,出现严重龟裂现象。极大地降低了混凝土抗渗、抗冻等混凝土的耐久性能。影响因素及应对措施混凝土离析的成因及应对措施众所周知,普通混凝土主要由水泥、水、砂石粗细骨料、外加剂等材料混合而成;泵送混凝土是在普通混凝土的基础上调整砂石粗细骨料级配、砂率和掺入一定量的粉煤灰混合而成。混凝土离析除与搅拌方法、搅拌时间长短有关外,一般的来讲,与混凝土拌合物的胶凝材料的优劣、用水量过大、碎石级配较差、减水剂掺量过大等关系更密切。水泥水泥是混凝土中最主要的胶凝材料,水泥质量的稳定直接影响着混凝土质量的稳定。水泥质量的变化将会导致混凝土出现离析的现象,而且水泥中有多种因素影响混凝土拌合物性能。水泥细度的变化众所周知,水泥的细度越高,其活性越高,水泥的需水量也越大,同时水泥细度越大,其水泥颗粒对混凝土减水剂的吸附能力也越强,极大的减弱了减水剂的减水效果。因此,在实际生产中,当水泥的细度大幅度降低时,混凝土外加剂的减水效果将得到增强,在外加剂掺量不变的情况下,混凝土的用水量将大幅度减少。水泥细度的下降,容易造成混凝土外加剂的过量,引起混凝土产生离析现象。而且这种离析通常发生在减水剂掺量较高的高强度等级混凝土中。水泥中含碱量变化碱含量对水泥与外加剂的适应性影响很大,水泥含碱量降低,减水剂的减水效果增强,所以当水泥的含碱量发生明显的变化时,有可能导致混凝土在黏度、流动度方面产生较大的影响。水泥存放时间的影响水泥是一种水硬性胶凝材料,如果存放不好,极易受潮,水泥受潮后需水量将降低;同时水泥存放时间越长,水泥本身温度有所降低,水泥细粉颗粒之间经吸附作用互相凝结为较大颗粒,降低了水泥颗粒的表面能,削弱了水泥颗粒对减水剂的吸附,在混凝土试验时往往表现为减水剂的减水效果增强,混凝土新拌合物出现泌浆、沉底的现象。在实际生产中,如果使用长时间存放的水泥,配合比不予调整,极容易造成混凝土的离析现象。当然,水泥存放时间对不同品种的水泥其影响是不一致的,这需要通过试验去了解。 综上所述可以看出,水泥中影响混凝土和易性的因素是很多的,也较为复杂,但不管是何种因素的影响,其表现出来的结果是相同的,(1)水泥需水量的变化;(2)水泥与外加剂的适应性变化。因此,如果是因为水泥的原因导致混凝土的离析,一般的都可以采取以下措施解决:(1)水泥进厂后,必须按要求试验项目进行检测,特别注意水泥的需水量情况,发现需水量异常时,及时做水泥与现使用的外加剂的适应性试验。必要时重新做混凝土配合比试验。(2)在保证混凝土水灰比不变的前提下(基本能保证混凝土的28 d强度),适当的调整减水剂的用量。(3)在保证强度的基础上,改用粉煤灰等掺合料的用量较大的配合比进行生产(商品混凝土公司应具备相同强度等级的不同配比),这必须以试验为基础。(4)用Ⅰ、Ⅱ粉煤灰等少量取代水泥,将能很好的控制混凝土的离析现象,改善混凝土和易性。外加剂混凝土中使用的外加剂,大多是由减水剂同其他产品如引气剂、缓凝剂、保塑剂等复合而成的多功能产品,是泵送混凝土不可或缺的重要材料,外加剂的掺入极大地改善混凝土拌合物的性能,但外加剂使用不当将可能导致混凝土的离析。(1)如果混凝土减水剂的掺量过大,减水率过高,单方混凝土的用水量减少,有可能使减水剂在搅拌机内没有充分发挥作用,而在混凝土运输过程中不断的发生作用,致使混凝土到现场的坍落度大于出机时的坍落度。此种情况极易造成混凝土的严重离析。且常表现在高强度等级混凝土中,对混凝土的危害极大。(2)外加剂中缓凝组分、保塑组分掺量过大,特别磷酸盐或糖类过量,也容易造成混凝土出现离析现象。当由于外加剂的原因造成混凝土的离析时,可从以下几方面进行调整:(1)调整配合比,降低减水剂的用量;(2)在混凝土外加剂中复合一定量的增稠剂;(3)在外加剂中复合一定量的引气剂,可增强混凝土的粘聚性,提高混凝土的抗离析性;(4)在混凝土试配时,应使混凝土在静态的条件下有20~30 mm的坍落度损失(1h),在实际生产中混凝土不易出现离析现象。粉煤灰粉煤灰是混凝土重要的掺和料之一,虽然用量很少,但在混凝土中掺入适量粉煤灰能极大改善混凝土和易性、密实性及强度性能。优质的粉煤灰如细度在20~8范围内,是配制混凝土的理想材料,能取代10%~30%的水泥用量,极大的降低了混凝土生产成本。若粉煤灰质量波动较大,增加了混凝土质量控制的难度,有时会造成混凝土出现离析的情况。(1)当粉煤灰的质量突然变好时(如细度从19%变为4%),粉煤灰的需水量降低很大,容易造成混凝土出现突然离析的现象;(2)同样当粉煤灰的质量突然变差时(如细度从19%变为38%),由于粉煤灰的很大一部分重量已失去胶结料的功能,因而外加剂相对胶结料掺量实际上已经提高了,所以会出现混凝土的离析现象。对于粉煤灰应采取如下措施:(1)加强检测,最好能对每车进厂的粉煤灰对进行检测,对不合格的材料坚决不能进场,起到预防作用。(2)调整粉煤灰的用量,选用掺量较低的配合比进行生产。(3)当粉煤灰质量较好情况,可适当的减少用水量,加强搅拌。或选用外加剂掺量较低的配合比进行生产。砂、石骨料砂石料是混凝土中用量最大的材料,砂石料的质量直接影响混凝土的质量,砂石质量的波动容易造成混凝土的离析,而且其造成离析的因素是多方面的。(1)碎石粒径增大、级配变差、单一级配都容易造成混凝土的离析现象。(2)砂子中的含石量过大、特别是含片状石屑量过大将严重影响混凝土的和易性,导致混凝土的严重离析。(3)砂石的含水率过高(特别是砂子含水率过高,大于10%),将使混凝土的质量难以控制,容易出现混凝土离析现象。由于砂子中含水过大,砂子含水处在过饱和状态,当混凝土拌合料在搅拌机中搅拌时,砂子表层毛细管中的含水不能够及时的释放出来,因此在搅拌时容易使拌合水用量过大;同时混凝土在运输过程中,骨料毛细管中的水不断的往外释放,破坏了骨料与水泥浆的粘结,造成混凝土的离析泌水。(4)砂石的含泥量过大将使水泥浆同骨料的粘结力降低,水泥浆对骨料的包裹能力下降,导致骨料的分离,引起混凝土离析现象。 对于由骨料的原因导致的混凝土离析的现象,可采取以下措施进行调整。(1)为避免因骨料的问题造成混凝土的离析问题,首先应以预防为主,严格骨料进场的检查制度,保证骨料的质量。(2)针对以上原因的第1条原因,可以适当的提高砂率来调整混凝土配合比,解决离析问题。(3)对于因骨料中含片状石屑过大造成的离析问题,单靠调整砂率是不能解决问题的,应提高混凝土胶结材料(特别是掺合料的用量),同时调整外加剂用量。(4)对于应骨料含水率问题造成的混凝土离析问题应采取延长搅拌时间的手段来解决。提高粉煤灰等掺合料的用量对控制这类离析现象也很有效果。其他以上分析了许多有关混凝土离析的原因,但造成混凝土离析的原因远不止这些,如水泥用量、水泥及掺合料品种、计量等问题都是引起混凝土离析的原因。在平时工作中,应注意积累,加强细节的管理,遇到问题及时解决。